Capacitors are essential components in modern electronics, playing a critical role in various applications from power supply circuits to signal processing. Understanding how capacitors are made can provide insights into their functionality and importance in electronic devices. In this article, we will explore the manufacturing process of capacitors, the materials used, and the different types of capacitors available in the market. By the end of this guide, you will have a thorough understanding of how capacitors are made and their significance in the electronic world.
The capacitor is a passive electrical component that stores electrical energy in an electric field, allowing it to release that energy when needed. From simple circuits to complex devices, capacitors are crucial in managing energy flow. This article aims to break down the intricacies of capacitor manufacturing while adhering to the principles of Expertise, Authoritativeness, and Trustworthiness (E-E-A-T).
Whether you are an electronics enthusiast, a student, or a professional in the field, understanding the manufacturing process of capacitors offers valuable knowledge. This information is particularly relevant in today's fast-paced technological landscape, where capacitors continue to evolve alongside advancements in electronic devices.
Table of Contents
- What Are Capacitors?
- Types of Capacitors
- Materials Used in Capacitor Manufacturing
- The Capacitor Manufacturing Process
- Quality Control in Capacitor Production
- Applications of Capacitors
- Future of Capacitor Technology
- Conclusion
What Are Capacitors?
Capacitors are two-terminal passive components that store electric charge. They consist of two conductive plates separated by an insulating material known as a dielectric. When a voltage is applied across the plates, an electric field is created, allowing the capacitor to store energy.
Capacitors are characterized by their capacitance, which measures the ability to store charge. The unit of capacitance is the farad (F), and capacitors can be found in various capacitance values, ranging from picofarads (pF) to farads.
Given their unique properties, capacitors are used in numerous applications, including:
- Energy storage
- Signal filtering
- Tuning circuits
- Power factor correction
Types of Capacitors
Capacitors come in various types, each designed for specific applications. The most common types include:
- Electrolytic Capacitors: These capacitors have a higher capacitance value and are polarized, meaning they must be connected in a specific direction.
- Ceramic Capacitors: Known for their stability and reliability, ceramic capacitors are non-polarized and available in various capacitance values.
- Tantalum Capacitors: Tantalum capacitors offer high capacitance in a small package and are often used in compact electronic devices.
- Film Capacitors: These capacitors use a thin plastic film as the dielectric and are known for their low losses and high stability.
Materials Used in Capacitor Manufacturing
The manufacturing process of capacitors involves various materials, each serving a specific purpose. The key materials include:
- Conductive Plates: Typically made from aluminum or tantalum, these plates serve as the electrodes for storing electric charge.
- Dielectric Materials: The choice of dielectric material significantly affects a capacitor's performance. Common materials include ceramic, aluminum oxide, and plastic films.
- Electrolytes: In electrolytic capacitors, a liquid or gel electrolyte is used to enhance capacitance.
The Capacitor Manufacturing Process
The manufacturing of capacitors involves several key steps:
1. Preparation of Materials
The first step in the manufacturing process is preparing the conductive plates and dielectric materials. The plates are cut to size, and the dielectric is processed to achieve the desired thickness and properties.
2. Layering
In many capacitor types, the conductive plates and dielectric layers are stacked or rolled together. This layering process is crucial for achieving the desired capacitance and voltage ratings.
3. Assembly
Once the materials are layered, the assembly process begins. For electrolytic capacitors, the electrolyte is introduced, and the capacitor is sealed to prevent leakage.
4. Testing and Quality Control
After assembly, capacitors undergo rigorous testing to ensure they meet quality standards. Parameters such as capacitance, voltage rating, and leakage current are measured and verified.
Quality Control in Capacitor Production
Quality control is vital in capacitor manufacturing to ensure reliability and performance. Manufacturers implement strict testing protocols, including:
- Electrical Testing: Capacitors are tested for capacitance, ESR (Equivalent Series Resistance), and leakage current.
- Environmental Testing: Capacitors are subjected to temperature and humidity tests to assess their performance under various conditions.
- Lifetime Testing: Accelerated aging tests are conducted to predict the lifespan of capacitors.
Applications of Capacitors
Capacitors are used in a wide array of applications, including:
- Consumer Electronics: From smartphones to televisions, capacitors play a vital role in energy management.
- Automotive: Capacitors are used in electric vehicles for energy storage and power management.
- Industrial: Capacitors are crucial in machinery and power systems for filtering and energy storage.
Future of Capacitor Technology
As technology advances, the demand for capacitors continues to grow. Future developments may include:
- Higher energy densities and capacitance values
- Improved dielectric materials for better performance
- Integration with renewable energy systems
Conclusion
In conclusion, capacitors are indispensable components in modern electronics, with a manufacturing process that involves careful selection of materials and rigorous testing. By understanding how capacitors are made, we can appreciate their role in the devices we use daily. If you found this article informative, feel free to leave a comment, share it with others, or explore more articles on our site!
Thank you for reading, and we look forward to seeing you again for more insightful articles!
Article Recommendations
- Balanced Lifestyle_0.xml
- Outdoor Propane Heater Table Top
- Hig Roberts
- Light Therapy
- How Long Do Horses Live
- Mary Anne Macleod Trump
- Personal Wifi
- How Old Is Adriana Lima 2024
- Cost To Extend Garage
- Creative Solutions_0.xml
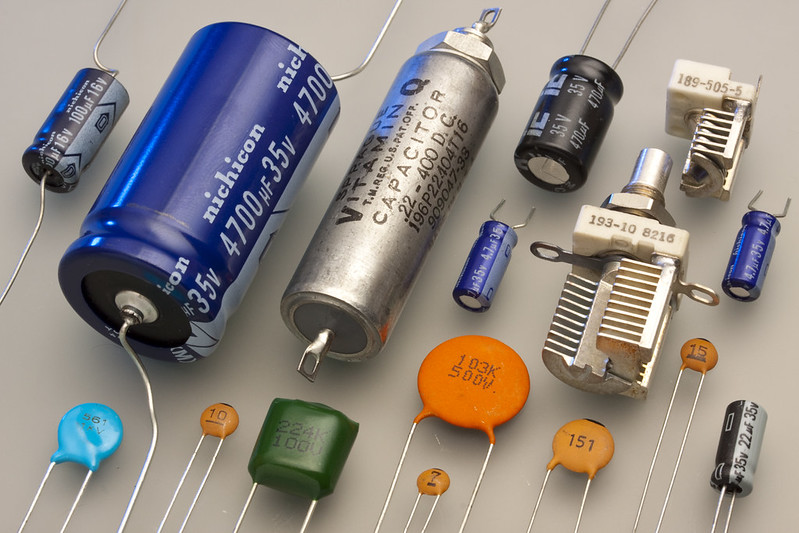

