DCS stands for Distributed Control System, a vital component in industrial automation that enhances efficiency and control. In the modern industrial landscape, understanding the role of DCS is essential for professionals and enthusiasts alike. This article delves into the intricacies of DCS, including its definition, components, advantages, and various applications across industries. Whether you are an engineer, technician, or simply curious about industrial systems, this comprehensive guide will provide you with the necessary insights.
The Distributed Control System (DCS) is pivotal in managing complex industrial processes, allowing for centralized control while distributing the operational load across various subsystems. This decentralized approach enhances reliability and flexibility, making DCS a preferred choice in industries such as oil and gas, chemical manufacturing, and power generation. As we explore the various aspects of DCS, you will gain a clearer understanding of its significance and functionality.
In this article, we will cover essential topics such as the architecture of DCS, its components, and how it integrates with other systems. Additionally, we will discuss the advantages of using DCS over traditional control systems and provide real-world examples of its applications. Let's dive deeper into the world of Distributed Control Systems.
Table of Contents
- What is DCS?
- Components of DCS
- Architecture of DCS
- Advantages of DCS
- Applications of DCS
- DCS vs SCADA
- Future of DCS
- Conclusion
What is DCS?
DCS, or Distributed Control System, refers to a control system that utilizes distributed control elements rather than a centralized control system. The primary objective of a DCS is to manage complex, large-scale industrial processes efficiently and reliably. A DCS typically consists of various control modules that communicate with each other over a network, allowing for real-time monitoring and control of processes.
Key Features of DCS
- Decentralized control architecture
- Real-time data monitoring and feedback
- Improved reliability and redundancy
- Scalability for expanding operations
Components of DCS
The architecture of a Distributed Control System is composed of several key components, each serving a specific function within the system. Understanding these components is crucial for grasping how DCS operates effectively.
1. Control Stations
Control stations are responsible for executing control algorithms and processing data. They can be located throughout the plant, allowing for localized control of various processes.
2. Field Devices
Field devices include sensors, actuators, and other instruments that gather data from the industrial process and feed it back into the control system for analysis and action.
3. Communication Network
The communication network facilitates the exchange of data between control stations and field devices, ensuring that information flows seamlessly throughout the system.
4. Human-Machine Interface (HMI)
The HMI provides operators with the tools to interact with the DCS, including visual displays, alarms, and control options.
Architecture of DCS
The architecture of a Distributed Control System can be broken down into three primary layers: the field layer, the control layer, and the supervisory layer.
1. Field Layer
The field layer consists of all the physical devices and instruments that monitor and control the process. This includes sensors, actuators, and other field equipment.
2. Control Layer
The control layer is where the main processing occurs. This layer includes control stations that execute control algorithms based on the data received from the field layer.
3. Supervisory Layer
The supervisory layer provides operators with a comprehensive view of the entire system. It includes the HMI and allows for monitoring, data analysis, and decision-making.
Advantages of DCS
Implementing a Distributed Control System offers numerous advantages over traditional centralized control systems. Here are some key benefits:
- Enhanced reliability due to redundancy in system components.
- Improved flexibility, allowing for easy modifications and expansions.
- Real-time data processing for quicker decision-making.
- Better system integration for different processes.
Applications of DCS
DCS is widely used across various industries, including:
- Oil and Gas: For monitoring and controlling drilling and production operations.
- Chemical Manufacturing: To manage complex chemical processes safely.
- Power Generation: For controlling the generation and distribution of electricity.
- Water Treatment: To ensure efficient management of water treatment processes.
DCS vs SCADA
While both DCS and SCADA (Supervisory Control and Data Acquisition) systems are used in industrial automation, they serve different purposes. DCS is focused on controlling complex processes, while SCADA is primarily used for monitoring and data collection. Understanding the differences between these systems can help determine the best solution for specific industrial needs.
Future of DCS
The future of Distributed Control Systems looks promising, with advancements in technology leading to enhanced capabilities. Integration with IoT (Internet of Things) and AI (Artificial Intelligence) is expected to revolutionize how DCS operates, providing even greater efficiency and control.
Conclusion
In summary, DCS stands for Distributed Control System, a crucial element in modern industrial automation. Its decentralized architecture, combined with real-time monitoring and data processing capabilities, makes it an invaluable tool for managing complex processes. As industries continue to evolve, the importance of DCS will only grow, paving the way for more efficient and reliable operations.
If you found this article informative, please leave a comment, share it with others, or explore more articles on our site. Your feedback is valuable to us!
Sources
- Control Global - Understanding DCS: Control Global
- ISA - Distributed Control Systems: ISA
- ResearchGate - DCS Applications: ResearchGate
Article Recommendations
- Financial Empowerment_0.xml
- Global Impact_0.xml
- Clr Soak Overnight
- Poker Face Sunglasses
- Convert Excel To Html Table
- Sheryl Lowe Age
- Lax Plane Spotting Locations
- Chevy S10 Steering Wheel
- Growth Hacking_0.xml
- Active Smooth Nail Polish

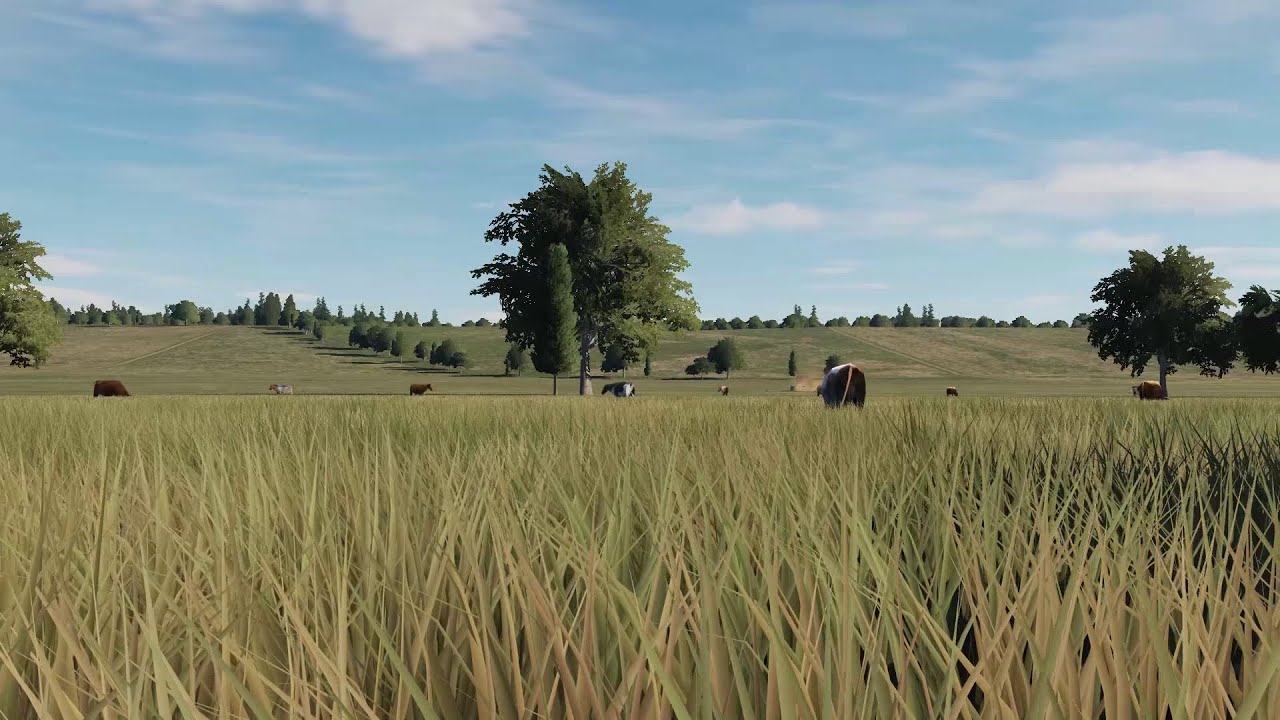
